Completata con successo la movimentazione integrale di 16 componenti strategici da un impianto all’altro, in un contesto minerario ad alta complessità operativa. Tra i carichi, un silo da 1.100 tonnellate e un frantumatore da 1.300 tonnellate movimentati con soluzioni di sollevamento e trasporto multidirezionale, nell’ambito di una strategia “unplug-and-play” che ha ridotto costi, tempi e discontinuità produttiva.
Nel comparto estrattivo, dove le infrastrutture rivestono un ruolo chiave per lo svolgimento delle attività quotidiane ad alta intensità, ogni impianto si confronta, dopo un ciclo operativo decennale, con la necessità di smobilitazione e rilocalizzazione delle attrezzature strategiche. In questo contesto si colloca il recente intervento condotto da Mammoet per Codelco, principale produttore cileno di rame, relativo al trasferimento di un sistema completo di frantumazione da un impianto all’altro, separati da un tracciato di 4,5 chilometri.
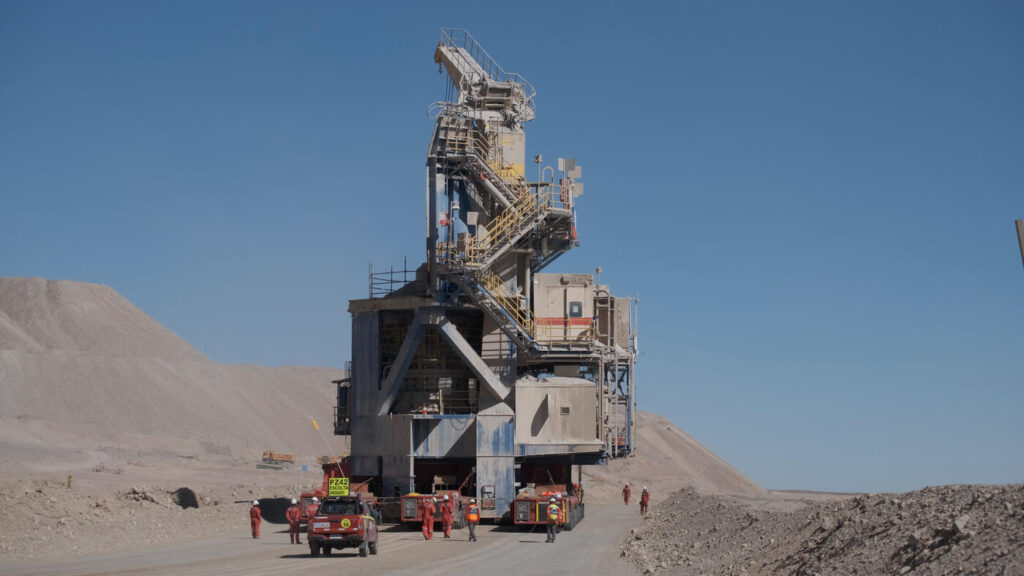
Il progetto ha riguardato 16 componenti, tra cui i sei elementi principali del frantumatore – i cosiddetti “big six” – per la prima volta oggetto, in questa configurazione, di una rilocalizzazione integrale da parte della società mineraria. L’incarico affidato a Mammoet ha incluso la consulenza tecnica completa per la definizione di tutte le fasi logistiche e ingegneristiche, con particolare attenzione alla scelta delle metodologie di sollevamento e trasporto eccezionale, in un’ottica di riduzione dei costi e contenimento del rischio.
“Abbiamo lavorato per un anno e mezzo alla pianificazione insieme a Codelco – spiega Vanessa Labana, Sales Manager di Mammoet – Abbiamo realizzato i tracciati, i disegni e risposto a tutte le problematiche tecniche, come pendenze, raggi di curvatura e larghezza della sede stradale per garantire il trasporto più rapido possibile”.
Le attività sono state rese possibili dalla capacità logistica e dalla disponibilità di flotta della rete internazionale Mammoet: moduli SPMT provenienti dalla Malesia, skidding systems dagli Stati Uniti, attrezzature complementari dalla Colombia. Ogni componente critico ha richiesto una metodologia personalizzata di estrazione, sollevamento e movimentazione, con uso combinato di martinetti a cremagliera, pattini da slittamento e travi di supporto rinforzate.
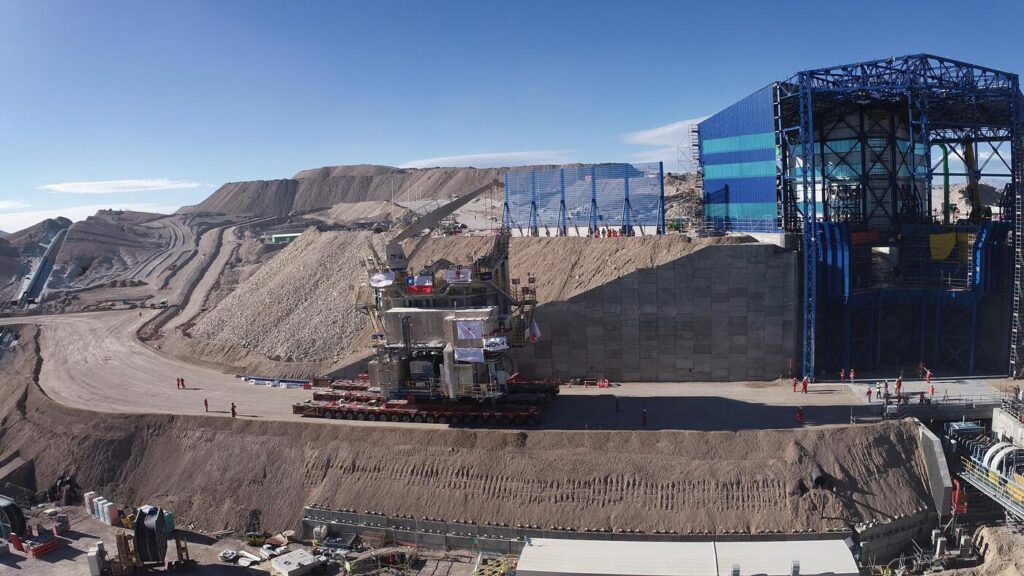
Tra gli elementi più impegnativi si segnalano oggetto un silo da 1.100 tonnellate e un frantumatore da 1.300 tonnellate, gestito come unità monolitica. “È stata una vera sfida – continua Labana – Abbiamo creato una trave di supporto su misura, rinforzata con piastre in piombo nei quattro punti di sollevamento, per evitare deformazioni durante il sollevamento”.
Il frantumatore è stato estratto dal suo alloggiamento tramite un sistema a slitte, sollevato fino a quota utile per l’inserimento degli SPMT e ancorato tramite sistemi di lashing per garantire stabilità durante il trasporto. È stata predisposta anche un’area dedicata per la rotazione a 180 gradi del carico, necessaria per l’orientamento finale in fase di posa. Nel sito di destinazione l’intera procedura è stata replicata in senso inverso, con abbassamento controllato e posizionamento finale tramite sistema combinato SPMT/slitte.
Particolarmente complessa anche la movimentazione dell’unità galleria, resa critica da una pendenza dell’1% del terreno: due martinetti idraulici posteriori, azionati in sequenza su tre fasi distinte, hanno garantito l’orizzontalità del carico durante tutta la fase di slittamento.
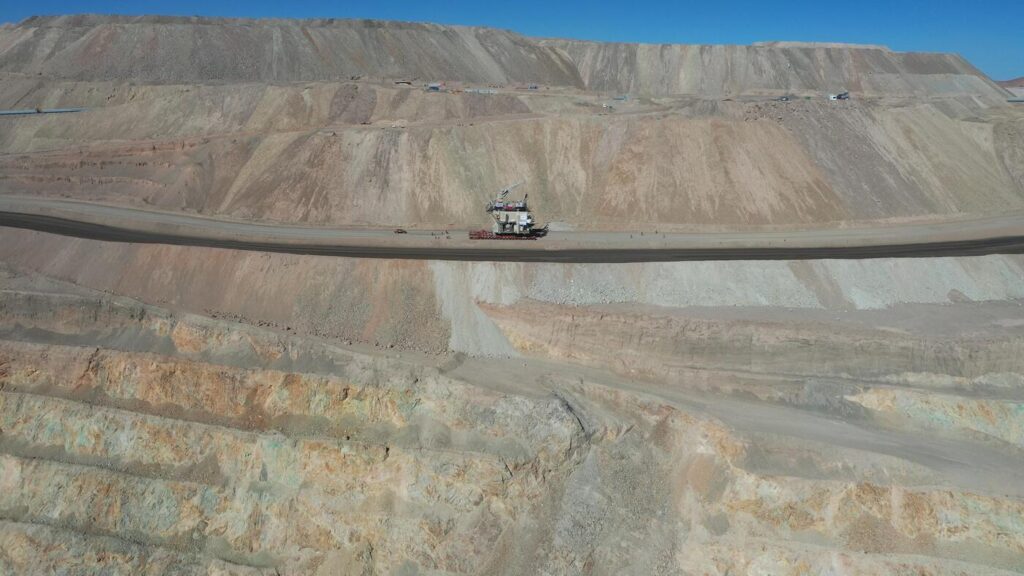
L’intera operazione si è conclusa in poco più di un mese, anticipando i tempi previsti e consentendo alla miniera di riprendere le attività produttive in tempi ridotti. Il successo dell’intervento è stato garantito dall’approccio integrato Mammoet, che ha incluso l’impegno di 70 operatori specializzati, 160 linee d’assi SPMT, 8 pattini da 500 tonnellate, 8 sistemi di sollevamento da 400 ton, oltre a travi dedicate, binari e ancoraggi customizzati.
“Se avessimo seguito una metodologia tradizionale, Codelco avrebbe dovuto tagliare e smontare completamente le attrezzature, impiegando molto più tempo – sottolinea Labana- È la prima volta che Codelco affronta un progetto simile. Ora hanno in noi un partner affidabile per i progetti futuri, grazie alla nostra esperienza, flotta e competenza tecnica”.