La realizzazione di pozzi di grande profondità mediante tecnologia raise boring rappresenta una delle sfide più complesse per l’industria mineraria, che richiede un connubio di progettazione meticolosa, competenze operative specialistiche e attrezzature all’avanguardia. Ne è testimonianza il recente traguardo raggiunto presso la miniera di Zinkgruvan, in Svezia, dove Drillcon Group ha completato con successo la perforazione di un pozzo di ventilazione profondo oltre 700 metri in un’unica fase operativa.
Il progetto, avviato nell’aprile 2024, si inserisce nell’ambito dell’ampliamento della miniera di Dalby, gestita da Zinkgruvan Mining, il sito estrattivo più meridionale del Paese. Il nuovo shaft rappresenta il quinto pozzo di ventilazione della miniera e il secondo realizzato in parallelo nella stessa campagna di lavori. La metodologia adottata è quella consolidata del raise boring tradizionale, con perforazione preliminare di un foro pilota e successiva alesatura ascendente attraverso una testa di 4,1 metri di diametro.
La particolarità di questa operazione risiede tuttavia nell’impiego delle più recenti soluzioni Sandvik Rock Tools. Il cantiere svedese ha visto il debutto operativo della punta pilota Sandvik RR890, della nuova versione della testa di alesatura 12EL e degli utensili da taglio di ultima generazione, equipaggiati con la tecnologia PowerCarbide brevettata dal costruttore nordeuropeo.
“Completare l’intero pozzo senza necessitĂ di sostituire i taglienti o effettuare manutenzione sulla testa di alesatura è un risultato straordinario – ha sottolineato Jonas Myrzell, Production Manager Raise Boring di Drillcon Group – Siamo entusiasti di aver avuto il supporto del team raise boring di Sandvik per raggiungere questo traguardo”.Â
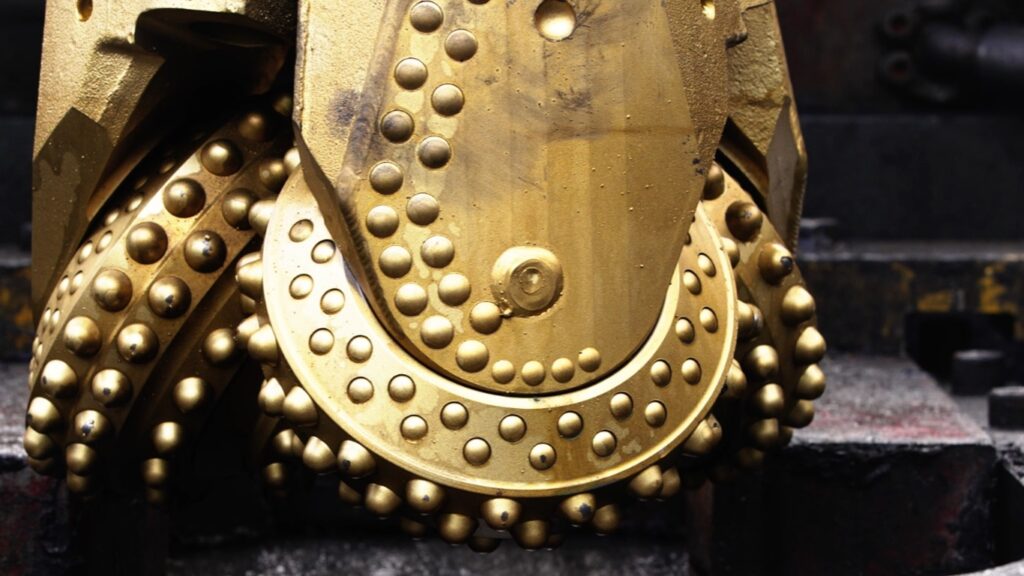
L’innovazione tecnologica applicata da Sandvik a questa fornitura è frutto di un percorso ingegneristico mirato a incrementare la produttività e la durata degli utensili, riducendo al contempo le interruzioni operative e i rischi per la sicurezza. La punta RR890 integra inserti PowerCarbide, protezioni rinforzate delle strutture portanti e un sistema di cuscinetti a rulli con doppia tenuta brevettata, concepito per prolungare la vita utile del componente e garantire una frattura della roccia più uniforme lungo l’intera tratta.
“Siamo estremamente soddisfatti dei risultati ottenuti da Drillcon in questo progetto e le elevate aspettative riposte nei nostri utensili ottimizzati per il raise boring sono state pienamente soddisfatte – ha dichiarato Russell Clayton, Product Manager Raise Boring presso Sandvik Rock Tools – Abbiamo inoltre testato insieme a Drillcon la prossima generazione di utensili da taglio con inserti PowerCarbide, puntando soprattutto sull’aumento della resistenza all’usura e sulla maggiore durata operativa. Abbiamo infine aggiornato il modello standard della testa di alesatura, basandoci sull’esperienza sul campo e sulla stretta collaborazione con Drillcon, per rispondere alle esigenze specifiche di questo raise”.
I dati operativi raccolti a fine cantiere confermano il valore del lavoro svolto: la punta pilota RR890 ha registrato un incremento del 69% delle prestazioni rispetto alle versioni precedenti Sandvik. Ancora più significativo il completamento della fase di alesatura lungo l’intera tratta di 700 metri senza che si rendesse necessario alcun intervento di sostituzione degli utensili da taglio.
Gli operatori coinvolti hanno descritto l’esperienza d’uso come estremamente fluida e affidabile, con una resa costante e un’aderenza perfetta alle previsioni di avanzamento giornaliero, fattori determinanti in un’attività ad alto rischio e complessità come il raise boring.
Particolare attenzione è stata riservata anche agli aspetti legati alla sicurezza e alla sostenibilitĂ economica delle lavorazioni. “La nostra prioritĂ assoluta in ogni operazione di raise boring è garantire la massima sicurezza per tutti gli operatori, mantenendo allo stesso tempo continuitĂ , velocitĂ di avanzamento e un approccio economicamente sostenibile in ogni fase della perforazione – ha concluso Myrzell – Abbiamo risparmiato oltre tre settimane di fermo per manutenzione e, soprattutto, evitato di esporre i nostri operatori ai rischi legati alla sostituzione degli utensili, alla movimentazione di attrezzature pesanti e ai potenziali pericoli derivanti dalla caduta di rocce”.